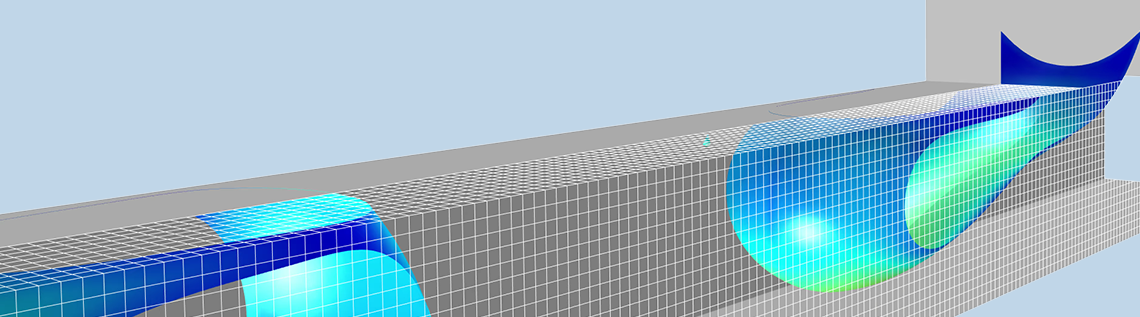
Multiphase flow may involve the flow of a gas-liquid, liquid-liquid, liquid-solid, gas-solid, gas-liquid-liquid, gas-liquid-solid, or gas-liquid-liquid-solid mixture. This series of blog posts mainly focuses on gas-liquid and liquid-liquid mixtures, although it also briefly discusses solid-gas and solid-liquid mixtures. We will also review the models and modeling strategies that are available in the CFD and Microfluidics modules.
Multiphase Flow Modeling on Different Scales
The study of multiphase flows with mathematical modeling may be done at several scales. The smallest scale can be around fractions of micrometers, while the largest scales are up to meters or tens of meters. These scales can span about eight orders of magnitude, where the largest length scale may be a hundred million times larger than the smallest scales. This implies that it is numerically impossible to resolve multiphase flows from the smallest to the largest scales using the same mechanistic model throughout the whole range of scales. For this reason, the modeling of multiphase flow is usually divided into different scales.
On the smaller scales, the shape of the phase boundary may be modeled in detail; for example, the shape of the gas-liquid interface between a gas bubble and a liquid. Such models may be referred to as separated multiphase flow models in the COMSOL® software. Methods used to describe such models are usually referred to as surface tracking methods.
On the larger scales, it is impossible to solve the model equations if the phase boundary has to be described in detail. Instead, the presence of the different phases is described using fields, such as volume fractions, while interphase effects such as surface tension, buoyancy, and transport across phase boundaries are treated as sources and sinks in the model equations of so-called dispersed multiphase flow models.
Separated multiphase flow models describe the phase boundary in detail, while dispersed multiphase flow models only deal with volume fractions of one phase dispersed in a continuous phase.
The figure above shows the principal difference between the two approaches for separated and dispersed multiphase flow models. In both exemplified cases, a function, Φ, is used to describe the presence of the gas and liquid phases. However, in the separated multiphase flow model, the different phases are exclusive, and there is a sharp phase boundary between them where the phase field function, Φ, changes abruptly. The phase field function does not have a physical meaning other than keeping track of the location of the phase boundaries.
In the dispersed multiphase flow model, the function Φ describes the local average volume fraction of gas, the dispersed phase, in the liquid, the continuous phase. The average volume fraction can smoothly find values between 0 and 1 everywhere in the domain, signifying if there are small or large amounts of bubbles in the otherwise homogenized domain. In other words, in the dispersed multiphase flow models, the gas and liquid phases can be defined in the same point in space and time, while in the separated multiphase flow models, there is either gas or liquid at a given point and time.
Separated Multiphase Flow Models
There are three different interface tracking methods in the COMSOL Multiphysics® software for separated multiphase flow models:
- Level set
- Phase field
- Moving mesh
The level set and phase field methods are both field-based methods in which the interface between phases is represented as an isosurface of the level set or phase field functions. The moving mesh method is a completely different approach to the same problem. With this approach, the phase boundary is modeled as a geometrical surface separating two domains, with one phase on each side in the corresponding domains.
The field-based problems are usually solved on a fixed mesh. The moving mesh problems are obviously solved using a moving mesh.
The animation below shows the results from a model in which an emulsion is produced in a T-shaped microchannel, where the problem is solved with the phase field method. We can see in this animation that the phase boundary does not coincide with the faces and edges of the mesh. The phase boundary is represented by the isosurface of the phase field function.
The finite element mesh does not have to coincide with the phase boundary between two phases in the phase field and level set methods.
In contrast, the figure below shows the verification model of a rising bubble with moving mesh. The mesh follows the shape of the phase boundary and the edges coincide with this boundary. We can also see the drawback of the moving mesh model. The bubble deforms to such an extent that two secondary bubbles detach from the mother bubble. At this point, the original phase boundary has to be divided into several boundaries. The logic for that is not completely straightforward and this is not yet implemented in the COMSOL® software. Hence, the moving mesh method in the COMSOL® software cannot deal with topology changes. The phase field methods do not have this drawback and can handle any changes in shape of the phase boundary.
The rising bubble verification problem. A topology change occurs when two secondary bubbles break away from the mother bubble.
When Do We Use Field-Based Methods Vs. Moving Mesh?
Moving mesh methods allow for a higher accuracy for a given mesh. The fact that we can apply forces and fluxes directly on the phase boundary is an advantage in this respect. The field-based methods require a dense mesh around the interphase surface in order to resolve the isosurface that defines this surface. It is difficult to define an adaptive mesh that accurately follows the isosurface, which leads that the mesh usually has to be dense in a large volume around the isosurface. This lowers the performance of the field-based methods in relation to moving mesh for the same accuracy. So, when do we use the different methods?
- For microfluidic systems where topology changes are not expected, then the moving mesh method is usually preferable
- In cases where topology changes are expected, then a field-based method has to be used:
- When the effects of surface tension are large, then the phase field method is the preferred method
- When surface tension can be neglected, then the level set method is preferred
Separated Multiphase Flow Models and Turbulence Models
In cases where turbulence models are used, the details of the flow are lost, since only the mean velocity and pressure are resolved. With this in mind, effects of surface tension also become less important for the macroscopic description of the flow. Since turbulence also implies that the flow is relatively vigorous, also at the surface, it is almost impossible to avoid topology changes. Hence, for turbulent flow models and separated multiphase flow combinations, the level set method is preferred. Both the level set and phase field methods can be combined with all turbulence models in COMSOL Multiphysics, as seen in the figure and animation below.
All turbulence models can be combined with the phase field and level set methods for two-phase flow in COMSOL Multiphysics.
Two-phase flow with water and air in a reactor modeled using the level set method in combination with the k-e turbulence model.
Dispersed Multiphase Flow Models
In cases where the phase boundaries cannot be resolved due to their complexity, dispersed multiphase flow models have to be used.
The CFD Module provides four different (in principle) models:
- Bubbly flow model
- For small volume fractions of a light phase in a denser phase
- Mixture model
- For a small volume fraction of a dispersed phase (or several dispersed phases) in a continuous phase that has about the same density as the dispersed phase or phases
- Euler–Euler model
- For any type of multiphase flow
- Can handle any type of multiphase flow also dense particles in gases; for example, in fluidized beds
- Euler–Lagrange models:
- For a relatively small number (tens of thousands, not billions) of bubbles, droplets, or particles suspended in fluid
- Each bubble, particle, or droplet is modeled with an equation that defines the force balance of each particle in the fluid
When Do We Use the Different Dispersed Flow Multiphase Flow Models?
Bubbly Flow
The bubbly flow model is obviously used for gas bubbles in liquids. Since the momentum contribution from the dispersed phase is neglected, the model is only valid when the dispersed phase has a density that is several orders of magnitude smaller than the continuous phase.
Mixture
The mixture model is similar to the bubbly flow model, but it accounts for the momentum contribution of the dispersed phase. It is commonly used for modeling gas bubbles or solid particles dispersed in a liquid phase. The mixture model can also handle an arbitrary number of dispersed phases. Both the mixture model and the bubbly flow model assume that the dispersed phase is in equilibrium with the continuous phase; i.e., the dispersed phase cannot accelerate relative to the continuous phase. Hence, the mixture model cannot handle large solid particles dispersed in a gas.
The mixture model used to model 5 different sizes of bubbles as the multiphase flow mixture is forced through an orifice. The shear in the flow causes larger bubbles to break up into smaller ones.
Euler–Euler
The Euler–Euler model is the most accurate dispersed multiphase flow model and also the most versatile. It can handle any type of dispersed multiphase flows. The dispersed phase is allowed to accelerate, and there is no real limit in the volume fractions for the different phases. However, it defines one set of Navier–Stokes equations for each phase.
In practice, the Euler–Euler model is only applicable for two-phase flow and even then, it is an expensive model with respect to computational cost (CPU time and memory). It is also relatively difficult to work with and requires good initial conditions to get convergence in the numerical solution.
Volume fraction of solid particles in a fluidized bed modeled using the Euler–Euler multiphase flow model.
Euler–Lagrange
When we have a few (tens of thousands but not billions) very small bubbles, droplets, or particles suspended in a continuous fluid, we may be able to use Euler–Lagrange models to simulate a multiphase flow system. These methods have the benefit of being relatively inexpensive, computation-wise. These models are usually also “nice” from a numerical point of view. They are therefore preferred when there is a relatively small number of particles of a dispersed phase in a continuous fluid.
Note that there are also methods to mimic a larger number of particles with Euler–Lagrange methods, using interaction terms and volume fractions that may mimic a system with billions of particles. These methods can be implemented in COMSOL Multiphysics, but they are not available in the predefined physics interfaces.
Euler–Lagrange multiphase flow models in COMSOL Multiphysics are available with the add-on CFD Module and Particle Tracing Module.
The mixture model is able to handle any combination of phases and is also computationally inexpensive. In most cases, it is advised that we start with this model, unless we deal with systems like fluidized beds (large particles with high density and high volume fractions of the dispersed phase), which can only be modeled with Euler–Euler models.
Dispersed Multiphase Flow Models and Turbulence
The dispersed multiphase flow models are approximative in their nature and fit very well with turbulence models, which are also approximative. It is possible to introduce interactions between dispersed phases and the continuous phase as well as between the bubbles, droplets, and particles in the dispersed phases. These interactions can have their origin in the turbulent eddies modeled with the turbulence model. The bubbly flow, mixture, and Euler–Lagrange multiphase flow models can be combined with all turbulence models in COMSOL Multiphysics. The Euler–Euler multiphase flow model is only predefined for the standard k-e turbulence models with realizability constraints.
The mixture model can be combined with any turbulence model in COMSOL Multiphysics.
Concluding Remarks
Solving the numerical model equations for multiphase flow may be a very demanding task, even with access to supercomputers. If there were no computer power limitations, the surface tracking methods would be used for all types of mixtures. In reality, these models are limited to microfluidics and for the study of free surfaces of viscous liquids.
The dispersed multiphase flow methods allow for the studying of systems with millions and billions of bubbles, droplets, or particles. But even the simplest dispersed multiphase flow models can generate very complex and demanding model equations. The development of these models into variations that are well adapted to describe specific mixtures has allowed for engineers and scientists to study multiphase flow with a relatively good accuracy and with reasonable computational costs.
Stay tuned as we continue our discussion of multiphase flow simulation on the blog!
Comments (30)
Thomas Radtke
April 3, 2020Ed,
thank your for this nice and readable summary of the available models for multiphase flow in Comsol. In the Euler-Lagrange section, you mention “that there are also methods to mimic a larger number of particles with Euler–Lagrange methods, using interaction terms and volume fractions that may mimic a system with billions of particles. These methods can be implemented in COMSOL Multiphysics, but they are not available in the predefined physics interfaces.”
Are there plans to include this functionality in coming Comsol versions. Or could you point to an example where this is added manually (maybe via support!?)?
Thanks a lot and looking forward to the next part of your multiphase series!
Thomas
Ed Fontes
April 28, 2020 COMSOL EmployeeDear Thomas,
The functionality will be included in a future version of COMSOL Multiphysics. But already now, you can include these effects manually in teh Particle Tracing Module. In the Fluid-Particle Interaction multiphysics coupling, there is an option for specifying a Force Multiplication Factor to let each simulated particle represent a larger number of physical particles. You can also use an Accumulator feature to extract a volume fraction which can be used to model density and collision effects in the fluid flow interface.
Best regards,
Ed
Saul Gomez
April 6, 2021Hi Ed,
I’m modelling particle separation according to density differences in a microfluidic channel. However, particle trajectories obtained are basically the same, no matter particle densities are different (also particle diameter differ). Is there a possibility that using this Accumulator feature could help me to achieve density-based separation? If it is, could you explain me how to implement it?
Best regards,
Saul
Ed Fontes
April 6, 2021 COMSOL EmployeeDear Saul,
This is really difficult for me to tell without seeing the model. Please contact our technical support for specific help for your case.
Best regards,
Ed
Jelle Snieder
August 21, 2020Hi Ed,
Thanks for this interesting blog. It has been very helpful for me for understanding the different multiphase methods in COMSOL. I am looking forward to the second part!
At this moment I am modelling a multiphase problem myself; spreading of a droplet of water (surrounded by air) between two flat plates. I am struggling a bit with selecting the ‘best’ multiphase method. I am interested in the propagation of the interface (droplet boundary) and in the future I foresee that topological changes will occur (merging of multiple droplets), when I will extend the model. So I am left with level-set and phase-field. Surface tension cannot be neglected; capillary effects are present. Could you please explain to me why phase-field is preferred over level-set if surface tension is relevant, as mentioned in your blog? From COMSOL support I understood that if the fluid motion is convection dominated, level-set is preferred (for computational reasons), while if it is diffusion dominated, phase-field is the way to go. What is your opinion?
Kind regards, Jelle
Ed Fontes
August 21, 2020 COMSOL EmployeeHi Jelle,
Thank you for your kind words. Right now I am working on the release of v5.6 but when this is done I will get back to writing on the second part. We actually have improved functionality for phase field and level set in the cases with large differences in density and viscosity for the involved fluids.
The reason why we recommend phase field for cases with large impact from surface tension is that the phase field method has better description of surface tension than level set. The phase field description is based on the excess energy at the interface between the phases. The level set is based on the evaluation of curvature, which is difficult to compute accurately, unless you have a very dense mesh or higher order base functions.
In addition, the phase field method works very well with no-slip conditions. With level set you have to apply a slip condition, which would probably influence your results in a somewhat non-physical way.
The reason why level set may be preferable for convection dominated problems is because it is a less computationally expensive method, and if there is a lot of convection, then the surface tension effect may be smaller compared to other forces (relatively).
Best regards,
Ed
Jelle Snieder
August 26, 2020Hi Ed,
Thanks for the response and explanation. I am looking forward to seeing the improved functionality for phase-field and level-set, as I am working with these large differences in density and viscosity for the involved fluids as well!
Kind regards, Jelle
Dan Abramson
October 27, 2020Thanks for the informative article. I need to simulate the non-isothermal fluid flow of a water/gas mixture in a heated pipe. However, I cant couple the Heat Transfer in Solids/Fluids with the 2-phase flow in the non-isothermal multi physics. Do you have any insight on this?
Ed Fontes
December 9, 2020 COMSOL EmployeeDear Dan,
1. For dispersed multiphase flow models, the multiphysics coupling is available in v5.6.
2. For separated multiphase flow, you will have to couple the heat transfer interface and the fluid flow interface manually. This is quite straightforward though.
Please contact support regarding item 2.
Best regards,
Ed
Ram Krishna
October 29, 2020Dear Ed,
I have followed many of your blogs here and they are quite informative. I have referred some of them in my journal articles too. I have an important suggestion for field-based models like Phase-field and Level-set methods. Comsol should provide clear guidelines for the setting of model parameters like Phase-field mobility, level-set parameter, or the mesh requirement for accurate resolution of the phases with sufficient literature references. I had to dig quite deeper into the literature to figure out the tuning of such parameters and I have found out that simulation results are highly dependent on these parameters especially for cases where the motion of contact lines is simulated.
Thank you,
Ram
Ed Fontes
December 9, 2020 COMSOL EmployeeDear Ram,
Thank you for your suggestions. We will surely take this into account for the next release.
Best regards,
Ed
Peter Cendula
December 8, 2020Thanks for the great overview.
For anyone looking for example of multiphase model of dispersed gases in liquid, I suggest looking at our work http://www.sciencedirect.com/science/article/pii/S0377042715000242.
Peter
Ed Fontes
December 9, 2020 COMSOL EmployeeDear Peter,
Thank you for sharing this.
Best regards,
Ed
Luca Leoni
January 7, 2021Hi Ed,
thanks for this helpful blog.
I was wondering about what boundary condition to use for a liquid-air free surface in an open channel. I am simulating a microfluidic multiphase laminar flow (non-Newtonian/air) in an open channel, using phase-field method. What would the most suitable boundary condition be for that free surface?
Thank you.
Kind regards,
Luca
Ed Fontes
April 6, 2021 COMSOL EmployeeHi Luca,
I do not completely understand your question. There is no boundary condition for the free surface using the phase field method. The isosurface of the phase field function represents the free surface. Please clarify what you mean.
Best regards,
Ed
sakhi tayeb
January 24, 2021Hello guys, I hope you are all fine and staying safe.
I am working on liquid foams (gas phase dispersed in liquid phase) , I’m wondernig which model should i use ?
Thanks in advance.
Ram Krishna
January 26, 2021If your problem involves topology changes (like bubble formation/breakup), use level-set or phase-field methods.
Oussamane Mebarako
February 2, 2021Ed,
I really found this summary helpful and interesting, that’s why I wanted to thank you so much first.
I will really be grateful to you if you could talk a little bit more about particles suspended by fluids and specially when we need to use the separated model.
Best regards,
Oussamane
Kareemulla Dudekula
February 3, 2021Ed,
I have just started exploring the COMSOL modeling capabilities; I am glad that I ran into your post; wonderful (comparative) summary of various modeling strategies. Thanks a ton! I am particularly interested in Euler-Euler modeling platform for (dense) gas-solid flows. Is is explicitly mentioned that the mixture model can handle any arbitrary number of dispersed phases, however, without allowing for acceleration (homogeneous flow?); I am wondering if the same advantage – being able to work with more than one accelerated dispersed phase – can be leveraged in Euler-Euler modeling too.
Your inputs will be greatly appreciated; I look forward to hearing from you.
Thanks & Regards,
Kareem
Ed Fontes
September 3, 2021 COMSOL EmployeeDear Kareemulla,
COMSOL’s Euler-Euler model implementation treat only two phases. In theory, you could model an arbitrary number of phases with the Euler-Euler model. However, in practice, already two phases are difficult enough to deal with, since you have one equation for the momentum balance in each space direction for each phase, one continuity equation minus one (n-1) for each phase, and one continuity equation for the mixture.
Best regards,
Ed
Ece Su Ildiz
July 18, 2021Dear Ed,
Thank you very much for detailed explanation. May I ask about how to simulate two-phase level-set method simulation with fluid in a microchannel and a cell flowing in it. I am using density and dynamic viscosity values accordingly but I stuck at what to choose reinitialization value (inlet flow is 20 ml/min) and how to see the cell will behave under shear stress (so I will do 2D shear stress simulation and change inlet flow rate). I want to see if cell is disaggregating or bending with the flow for different shear stress values in simulation. Thank you very much!
Best Regards,
Ece Su
Ed Fontes
September 3, 2021 COMSOL EmployeeDear Ece,
It is difficult yo help you with this specific model without seeing the actual model. Please contact our technical support for help.
Best regards,
Ed
Murat Özay
September 2, 2021Hi,
I want to simulate a biological Methanation process. In a Pipe I have 2 inlets and 1 outlet. In the first inlet should flow in water and in the second inlet should flow in a (hydrogen/carbon dioxid) mix. my goal is to obtain methane in the output by a chemical reaction. Wich Physics do i need for this Process?
Murat
Ed Fontes
September 3, 2021 COMSOL EmployeeDear Murat,
It looks like you could use the mixture model interface together with a multicomponent transport interface. But its is difficult to say without more details. Please contact technical support.
Best regards,
Ed
畅 刘
October 17, 2021Hi Ed,
I have learned a lot after reading your blog, thank you so much! I want to ask a question which is very similar to the example in “Studying Multiphase Flow and Liquid-Liquid Extraction in COMSOL Multiphysics®” that you introduced at the 2017 COMSOL seminar.
I am now simulating the liquid-liquid extraction process at the oil-water interface. Substance A will diffuse from the water into the oil. I use the level-set method to track the liquid-liquid interface, and use the TDS module to study the mass transfer process. In the new version of COMSOL, I can easily set the partition coefficient (K) of A in two phase through the “Partition Condition”, or use the “Thin Diffusion Barrier” to set the barrier of A through the water-oil interface (interfacial diffusion coefficient, D). My question is that COMSOL cannot set Partition Condition and Thin Diffusion Barrier at the same time, otherwise they will replace each other. The partition coefficient is the thermodynamic consideration of extraction, while the diffusion coefficient or interface mass transfer coefficient determines the extraction kinetics, and both should be indispensable. How can I set the distribution coefficient K and the interface diffusion coefficient D at the same time on interior boundaries separating two liquid phases? By the way, can you provide a tutorial on the liquid-liquid extraction process?
Looking forward to your reply, thank you!
Best regards,
Chang
Praveen Ravikumar
April 25, 2022Dear Ed,
Thank you for this wonderful blog on multiphase flows on COMSOL.
Currently, I am working with two-phase liquid -liquid slug flows in microchannels with an aim of studying the internal circulations within them using level set . The system is modelled based on the parameters in the paper attached ,where the channel diameter is 0.494mm and the bubble equivalent diameter is greater than 1. A system of glycerol and Air is considered initially before moving into liquid liquid systems.
To avoid the computational time,I am adopting a periodic boundary condition and a moving reference frame approach. To achieve that the wall must me moved with the final steady state bubble velocity.
Kindly let me know what are the ways in which the bubble velocity can be calculated accurately on COMSOL from the simulation.
https://doc.rero.ch/record/332818/files/10404_2015_Article_1566.pdf
RADHARAMANA GANESAN
January 2, 2023Hi Ed,
I’m working on the stability of nanobubble under the parameters such as PH and temperature. Which model should I use?
Amin Pi
March 17, 2023Hello Ed,
Thank you for the thorough explanation of multiphase problems.
I am trying to model a bubble collapse using level set or phase-field model. However, I am not sure whether the topology change could be captured correctly since it is the aim of the this study. I need to capture the jet formation of bubble collapse and subsequently couple it with another model to show its effect on an elastic membrane.
What is the best set of physics and mesh you would propose?
Regards,
Amin
Thiago Oliveira Cabral
April 7, 2023Hi, Ed! How are you?
Thank you so much for the clarifications in this blog! I’d like to ask you a question. I’m trying to model a gas-solid fluidized bed containing relatively large solid particles (diameters between 0.3-1 mm), with a geometry that resembles the one shown in your blog (a rectangle). The solid is almost 2000 times denser than the gas. I’m using the Euler-Euler model and I’m applying the Gidaspow model for the drag coefficient. I’m also ramping up gravity and the inlet gas velocity in time. The initial volume fraction of the dispersed phase in the bed is also being smoothed in space to avoid discontinuities. Even though I make those numerically friendly alterations, I’m not being able to make the model converge at all. It only works for much smaller solid particles. Would you share any tips on how can I succeed in this modeling? Thank you so much!
Dhairyadhar Bhelave
May 30, 2023Hi Ed. Thank you for the concise but accurate information. I have some additional issues. While running a multiphase simulation of liquid dispersed in the gas phase, I am not sure which model will be most accurate. Besides, if I use the mixture model, It allows us to input only the velocity of the phases as inlet boundary condition, while I wish to specify mass flow rates. Could you elaborate on these points?